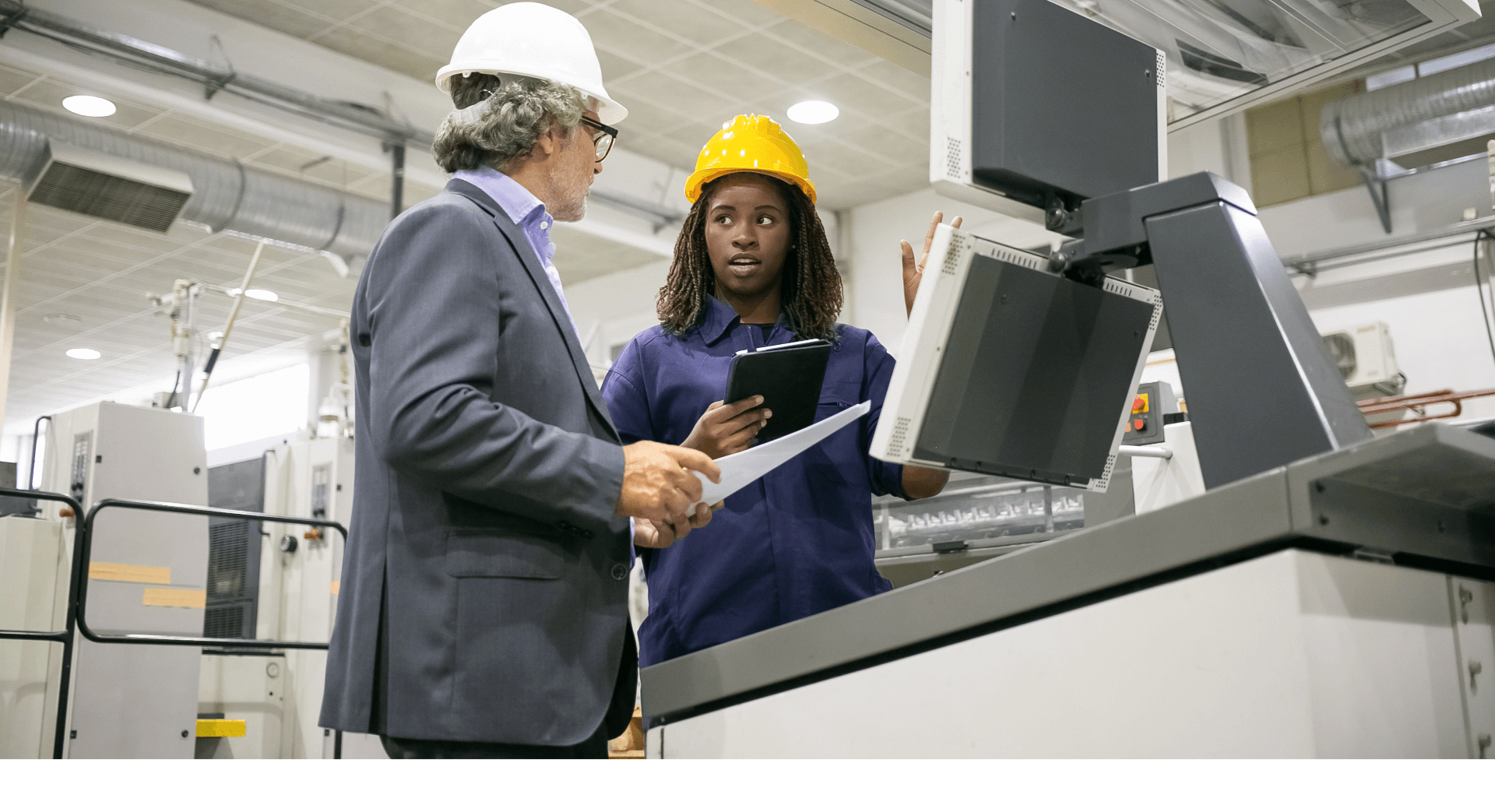
AIT Digital Maintenance Solution (DMS)
Finally spend more time preventing maintenance problems and failures from happening, and less time desperately reacting them after the fact!
Breakthroughs in AI-powered digital maintenance solutions (DMS) now enable operations managers to grasp the full power of their maintenance data and stop wasting time with spreadsheets, whiteboards, and hard-to-use maintenance management software.
email us at sales@automateit.net
or call 417.429.4320 | Toll Free 866.576.7584
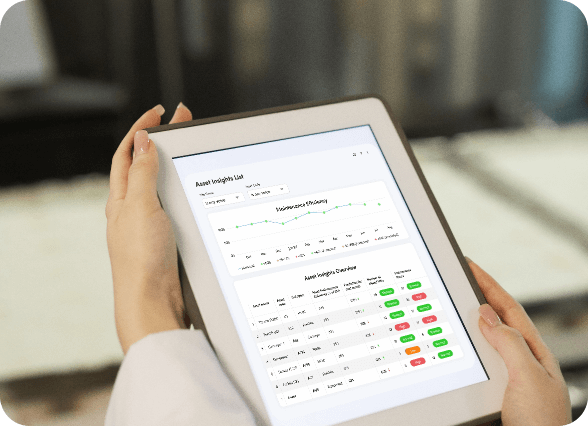
Juice-up your maintenance efficiency with AI-powered DMS
AutomateIT’s cloud-based DMS solution lets you plan, track, and optimize maintenance in seconds, empowering your team to keep uptime high and end maintenance headaches.
DMS sifts all your maintenance data including work and purchase orders, analyzes asset and work patterns for anomalies such as large uses of time or money, then presents results on a single dashboard so you can accurately prioritize and schedule — without the need for messy spreadsheets or paper!
And it has a self-learning capability that continuously improves accuracy so you can always you’re your maintenance with confidence.
We’ve put together this ROI Calculator to help you calculate your potential ROI on DMS and how fast it can start delivering you tangible bottom-line improvements.
DMS: the fastest way to drive tangible maintenance improvements
- Asset-related downtime cut by 27%
- Production and operating costs reduced by 10%
- Mean time to repair reduced by 20%
- Inspection times reduced by 73%
- Labor costs down by 44%
Source: IDC
Our DMS capabilities
Create, complete, and record work orders
Take care of your to-do list without limitations.
Make work requests with a few taps
Put an end to time-consuming, unclear, and ineffective work orders jobs are done faster and keep assets running at their best.
Simplify your work request process
Submit, then search, sort, prioritize, and track work requests through a single portal.
Schedule maintenance that runs like clockwork
Schedule maintenance using date, time, meter, event or condition-based triggers, and simplify schedules with nested PMs and multi-asset work orders.
Complete maintenance fast and flawlessly
Attach SOPs, task lists, photos, and suggested parts to work orders so technicians have everything to efficiently complete maintenance.
Track and report everything
See all work orders and everything about them in a couple of clicks, including completion rates, repair dates, total costs, follow-up tasks to failed inspections, and more.
Identify troublesome work orders
Analyze performance and spot what work is causing equipment failure, work delays, and compliance issues from your analytics dashboard.
Eliminate maintenance guesswork
Set up common failure codes to eliminate trial and error troubleshooting.